Autonomous electrical vessels – Cold ironing
Concept
This concept is the development of an on-board floating LNG power plant system in a new built (or retrofitted) open-type vessel or in a propelled barge. The project aims to solve the air pollution problem in highly touristic cruise ports (i.e. Piraeus, Heraklion, Santorini, Mykonos etc.). During the touristic season (i.e April-October) the cruise ships (and other types of touristic vessels) spend many hours within the ports, burning diesel or low sulfur oil as marine fuel (according the IMO regulation).
The idea is to provide these ships with electricity produced by an on-board floating LNG power plant system in a new built or retrofit open-type vessel/or barge. LNG is more economic efficient than Diesel and produces less emissions than any other fossil fuel.
The LNG will be stored in containers or in a large storage tank. This vessel will provide electricity power (cold ironing) to the cruise vessels, where there is no such current support (Piraeus) or where there is no alternative future solution – onshore facility (Santorini). The advantage of this vessel is that there is no need for the built-up of an onshore facility in the port to supply electricity to the cruise vessels. This can boost the applicability and marketability of this solution to a number of different areas in Greece.
Additionally, this plant will be equipped with batteries. The vessel will have the ability to connect to the electricity system power grid in order to:
For Piraeus:
•Sell excess “Green” electricity to the grid
•Store electricity from the grid during the night (low prices, increase system stability)
For the islands:
•Sell excess “Green” electricity to the island’s non-interconnected grid during the peak season and in emergencies (outage of a power plant, blackouts).
•Store electricity from the grid in order to increase the penetration of the existing renewable energy generation plants (Wind, Solar energy).
Main Characteristics
+Open Type vessel or propelled barge [80-100×15-30m] with LNG fuelled engines of 10-12 MW
+Onboard Containers LNG for fuel, using 2-4 containers 80-160m3 LNG or storage tank
+ Supplying LNG from DESFA’s Terminal Revythousa Island by trucks or feeder boat >=5 MW Power engine
+Electrical connection systems
+Software to handle electricity power supply
Cold Ironing: The role of ports in reducing shipping emissions
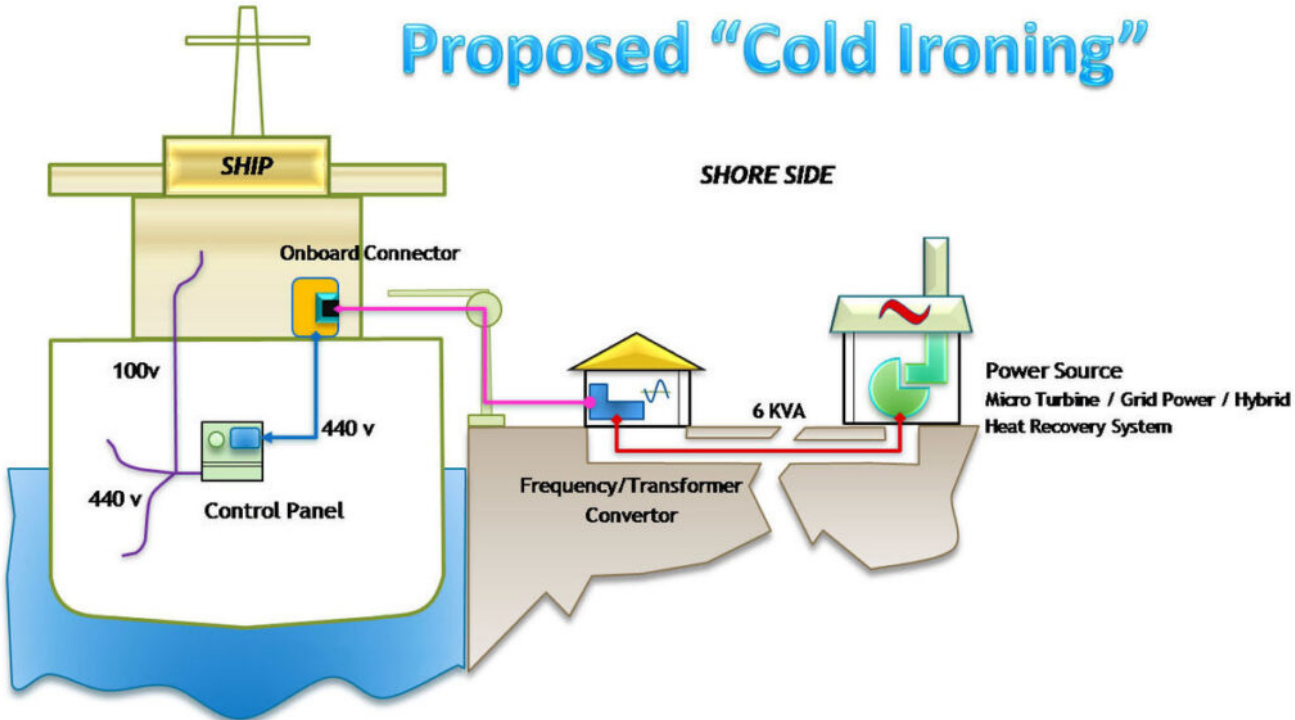
With the shipping industry entering a new, environmentally-friendly period, stakeholders in the maritime industry are seeking for ways to reduce their ships’ emissions. Apart from choosing green fuels and scrubbers, ports come to add another solution: Cold Ironing. This is the process of providing shoreside electrical power to a ship at berth, while its main and auxiliary engines are turned off.
How does cold ironing work
Cold ironing goes way back into shipping’s past, as it first appeared when all ships were using coal-fired engines. Specifically, when a ship was berthing at port, it did not have to continue to feed the fire, and the iron engines would cool down, going totally cold. This is from where this process took its name from.
Nowadays however, when ships are berthed, they use their auxiliary engines to support some basic functions. This must be taken into consideration, as it generates SOx, NOx, CO2 and particle discharge as well as noise and vibration.
To mitigate these issues, cold ironing comes to offer a solution. This technology is basically an anti-pollution measure, to reduce air pollution produced from diesel generators, through the use of shore electric power as an alternative.
During cold ironing, the ship turns off its engines while berthed and plugs into an onshore power source. The ship’s power load is then transferred to the shore-side power supply without disrupting onboard services.
With this process, emergency equipment, refrigeration, cooling, heating, lighting, and other equipment are still able to receive continuous electrical power, while the ship loads or unloads its cargo.
In fact, studies have found that by using this method, many environmental and social benefits are generated.
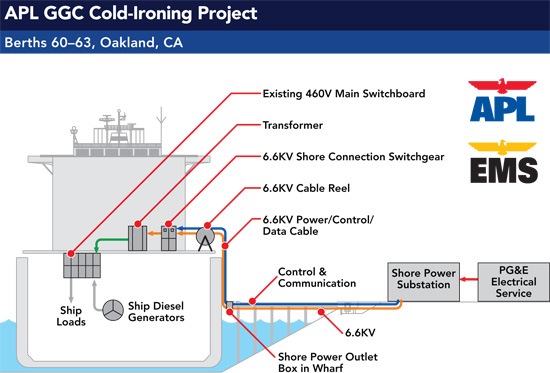
What we offer
•Advanced Assistance systems: Technology enables the crew to take the right actions at the right time, enhancing safety and efficiency by automating specific tasks and even new ship designs.
•Future of ship command systems: Merging the worlds of INS and IAS, we have developed a new generation of ship command systems that always enable the most efficient execution of tasks and best practices.
•Autonomous Short Sea Shipping: Applying autonomous solutions, we are disrupting inland and coastal short distance shipping to become a safer, greener, and more efficient link in the logistic chain.
•Navigation and DP solutions: With a lineage dating back to the 1960s, our Dynamic Positioning (DP) systems and specialised sensors technology have a long history of providing critical support and information to the bridge crew. We continue to develop, deliver, and stay at the forefront in this category
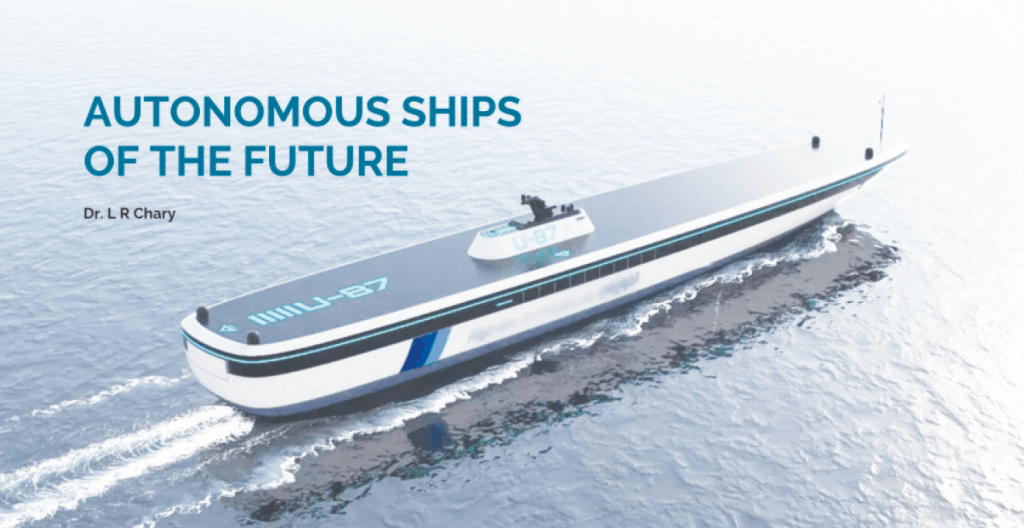
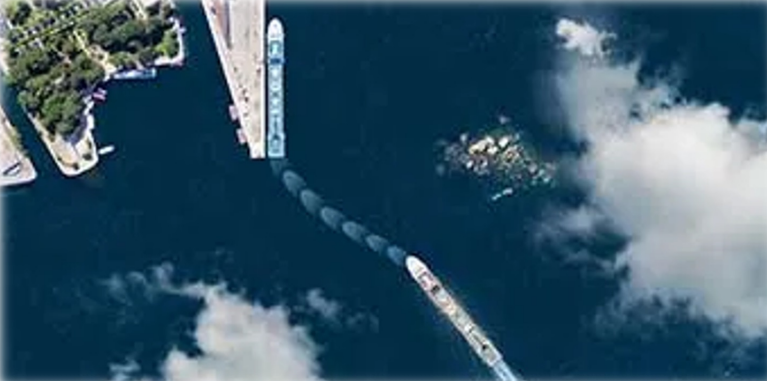